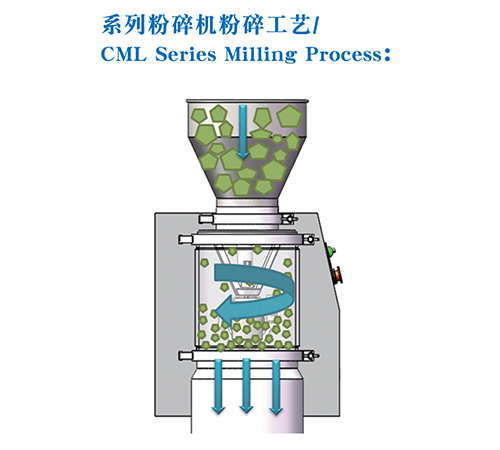
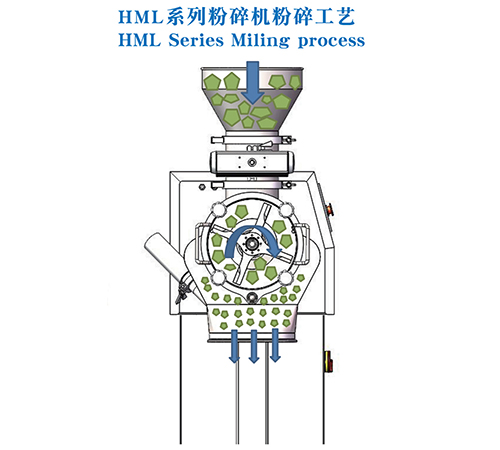
مخروط کی گھسائی کرنے والی
مخروطی ملز، یا مخروطی سکرین ملز کو روایتی طور پر دواسازی کے اجزاء کے سائز کو یکساں انداز میں کم کرنے کے لیے استعمال کیا جاتا رہا ہے۔ تاہم، وہ اختلاط، چھلنی اور بازی کے لئے بھی استعمال کیا جا سکتا ہے. وہ مختلف سائز میں آتے ہیں، بشمول ٹیبل ٹاپ لیبارٹری کے آلات سے لے کر پورے پیمانے پر، اعلیٰ صلاحیت والی مشینیں جو بڑے فارماسیوٹیکل پروسیسنگ آپریشنز کے لیے استعمال ہوتی ہیں۔
اگرچہ شنک ملز کے استعمال مختلف ہوتے ہیں، لیکن دواسازی میں ان کے استعمال کی طرف رجحان میں پیداوار کے دوران خشک مواد کو ڈی lumping کرنا شامل ہے۔ خشک ہونے سے پہلے گیلے دانے دار ذرات کا سائز بنانا؛ اور خشک دانے دار ذرات کو خشک ہونے کے بعد اور گولی لگانے سے پہلے ان کا سائز دینا۔
دیگر ملنگ ٹیکنالوجیز کے مقابلے میں، کون مل دواسازی کے مینوفیکچررز کو دیگر مخصوص فوائد بھی پیش کرتی ہے۔ ان فوائد میں کم شور، زیادہ یکساں ذرہ سائز، ڈیزائن کی لچک اور زیادہ صلاحیت شامل ہیں۔
آج مارکیٹ میں سب سے جدید ملنگ ٹیکنالوجی زیادہ تر تھرو پٹ اور مصنوعات کے سائز کی تقسیم پیش کرتی ہے۔ اس کے علاوہ، وہ متغیر چھلنی (اسکرین) اور امپیلر کے اختیارات کے ساتھ دستیاب ہیں۔ جب کم کثافت والے مواد کے ساتھ استعمال کیا جائے تو، ایک چھلنی سیدھی سلاخوں کے ساتھ ڈیزائن کی گئی ملوں کے مقابلے میں 50 فیصد سے زیادہ تھرو پٹ بڑھا سکتی ہے۔ کچھ معاملات میں، صارفین نے 3 ٹن فی گھنٹہ تک یونٹ کی پیداواری صلاحیت حاصل کی ہے۔
دھول سے پاک مخروطی ملنگ کا حصول
یہ بات اچھی طرح سے معلوم ہے کہ گھسائی کرنے سے دھول پیدا ہوتی ہے، جو آپریٹرز اور فارماسیوٹیکل پروسیسنگ ماحول کے لیے خاص طور پر خطرناک ہو سکتی ہے اگر دھول موجود نہ ہو۔ دھول پر قابو پانے کے کئی طریقے دستیاب ہیں۔
بن ٹو بن ملنگ ایک مکمل طور پر ان لائن عمل ہے جو شنک مل کے ذریعے اجزاء کو کھانا کھلانے کے لیے کشش ثقل پر انحصار کرتا ہے۔ تکنیکی ماہرین مل کے نیچے ایک ڈبہ رکھتے ہیں، اور مل کے اوپر براہ راست ایک ڈبہ مل میں مواد چھوڑتا ہے۔ کشش ثقل مواد کو گھسائی کرنے کے بعد براہ راست نیچے والے کنٹینر میں جانے کی اجازت دیتی ہے۔ یہ پروڈکٹ کو شروع سے ختم تک رکھتا ہے، اور ساتھ ہی ملنگ کے بعد مواد کی منتقلی کو آسان بناتا ہے۔
ایک اور طریقہ ویکیوم ٹرانسفر ہے، جو ایک آن لائن عمل بھی ہے۔ یہ عمل دھول پر مشتمل ہے اور اس عمل کو خودکار بھی بناتا ہے تاکہ صارفین کو اعلی کارکردگی اور لاگت کی بچت حاصل کرنے میں مدد ملے۔ ان لائن ویکیوم ٹرانسفر سسٹم کا استعمال کرتے ہوئے، تکنیکی ماہرین شنک کی چوٹ کے ذریعے مواد کو کھانا کھلا سکتے ہیں اور انہیں خود کار طریقے سے مل کے آؤٹ لیٹ سے نکال سکتے ہیں۔ اس طرح، شروع سے ختم تک، عمل مکمل طور پر منسلک ہے.
آخر میں، الگ تھلگ ملنگ کی سفارش کی جاتی ہے کہ گھسائی کے دوران باریک پاؤڈر رکھیں۔ اس طریقہ کے ساتھ، مخروط کی چکی دیوار کو ٹھیک کرنے والے فلینج کے ذریعے الگ تھلگ کرنے والے کے ساتھ ضم ہو جاتی ہے۔ شنک مل کی فلینج اور کنفیگریشن کون مل ہیڈ کو پراسیسنگ ایریا کے ذریعہ فزیکل تقسیم کرنے کی اجازت دیتی ہے جو الگ تھلگ سے باہر ہے۔ یہ ترتیب دستانے کے خانے کے ذریعے الگ تھلگ کے اندر کسی بھی صفائی کی اجازت دیتی ہے۔ یہ دھول کی نمائش کے خطرے کو کم کرتا ہے اور پروسیسنگ لائن کے دوسرے علاقوں میں دھول کی منتقلی کو روکتا ہے۔
ہتھوڑا ملنگ
ہتھوڑا ملز، جسے کچھ فارماسیوٹیکل پروسیسنگ مینوفیکچررز ٹربو ملز بھی کہتے ہیں، عام طور پر تحقیق اور مصنوعات کی ترقی کے ساتھ ساتھ مسلسل یا بیچ کی پیداوار کے لیے موزوں ہیں۔ وہ اکثر ایسے معاملات میں کام کرتے ہیں جہاں منشیات تیار کرنے والوں کو مشکل سے مل جانے والے APIs اور دیگر مادوں کے عین مطابق ذرات میں کمی کی ضرورت ہوتی ہے۔ اس کے علاوہ، ہتھوڑے کی چکیوں کو اصلاح کے لیے پاؤڈر میں پیس کر ٹوٹی ہوئی گولیوں کو دوبارہ حاصل کرنے کے لیے استعمال کیا جا سکتا ہے۔
مثال کے طور پر، معائنے کے بعد، کچھ تیار کردہ گولیاں مختلف وجوہات کی بنا پر صارف کے معیار کے مطابق نہیں ہو سکتی ہیں: غلط سختی، خراب شکل، اور زیادہ وزن یا کم وزن۔ ان صورتوں میں، مینوفیکچرر مواد پر نقصان اٹھانے کے بجائے گولیوں کو ان کے پاؤڈر کی شکل میں واپس ملنا منتخب کر سکتا ہے۔ گولیوں کو دوبارہ ملنا اور انہیں دوبارہ پیداوار میں متعارف کرانا بالآخر فضلہ کو کم کرتا ہے اور پیداواری صلاحیت میں اضافہ کرتا ہے۔ تقریباً تمام حالات میں جہاں گولیوں کا ایک بیچ تصریحات پر پورا نہیں اترتا، مینوفیکچررز اس مسئلے پر قابو پانے کے لیے ہتھوڑے کی چکی کا استعمال کر سکتے ہیں۔
ہتھوڑا ملیں 1,000 rpm سے 6,000 rpm تک کی رفتار سے کام کرنے کی صلاحیت رکھتی ہیں جبکہ 1,500 کلوگرام فی گھنٹہ تک پیداوار دیتی ہیں۔ اس کو حاصل کرنے کے لیے، کچھ ملیں ایک خودکار گھومنے والے والو سے لیس ہوتی ہیں جو تکنیکی ماہرین کو زیادہ بھرے بغیر اجزاء کے ساتھ ملنگ چیمبر کو یکساں طور پر بھرنے کی اجازت دیتی ہے۔ ضرورت سے زیادہ بھرنے کو روکنے کے علاوہ، اس طرح کے خودکار فیڈنگ ڈیوائسز ملنگ چیمبر میں پاؤڈر کے بہاؤ کو کنٹرول کر سکتے ہیں تاکہ عمل کی تکرار کو بڑھایا جا سکے اور گرمی کی پیداوار کو کم کیا جا سکے۔
کچھ زیادہ جدید ہتھوڑا ملوں میں دو طرفہ بلیڈ اسمبلی ہوتی ہے جو گیلے یا خشک اجزاء کی عملداری کو بڑھاتی ہے۔ بلیڈ کا ایک رخ خشک مواد کو ٹکڑے ٹکڑے کرنے کے لیے ہتھوڑے کا کام کرتا ہے، جب کہ چاقو نما سائیڈ گیلے اجزاء کے ذریعے کاٹ سکتی ہے۔ صارفین صرف ان اجزاء کی بنیاد پر روٹر کو پلٹتے ہیں جن کی وہ گھسائی کر رہے ہیں۔ مزید برآں، کچھ مل روٹر اسمبلیوں کو مخصوص مصنوعات کے رویے کے لیے ایڈجسٹ کرنے کے لیے الٹ دیا جا سکتا ہے جبکہ مل کی گردش میں کوئی تبدیلی نہیں ہوتی۔
کچھ ہتھوڑا ملوں کے لیے، پارٹیکل سائز کا تعین اس سکرین کے سائز کی بنیاد پر کیا جاتا ہے جو مل کے لیے منتخب کیا جاتا ہے۔ جدید ہتھوڑا ملیں مواد کے سائز کو 0.2 ملی میٹر سے 3 ملی میٹر تک کم کر سکتی ہیں۔ پروسیسنگ مکمل ہونے کے بعد، مل اسکرین کے ذریعے ذرات کو دھکیلتی ہے، جو مصنوعات کے سائز کو منظم کرتی ہے۔ بلیڈ اور سکرین حتمی مصنوعات کے سائز کا تعین کرنے کے لئے مل کر انجام دیتے ہیں۔
پوسٹ ٹائم: اگست 08-2022